Minimum quantity lubrication with internal feed
Aerosol Boosters are plug-and-play devices for the optimum lubrication of your tools with internal cooling channels. The dosage is self-regulating in some models and thus adjusts itself automatically for each tool used. In this way, operating errors are avoided by principle and the set-up effort is reduced to the minimum. In consequence, aerosol boosters combine high reliability with the simplest possible operation.
Product overview
Characteristics
- Single-channel system: transport of the aerosol in a standard hose line
- Thanks to nanometer-sized oil particles in the aerosol, also suitable for lubricating the smallest tools at high revolutions speeds
- Supply of several spindles by one MQL device possible
- Electrical, pneumatic or manual control possible
- Automatic filling of several MQL units from a central reservoir possible
- Shortest response times: reliable lubrication from the first second even after tool changes or machine downtimes
- Worry-free setup: no programming of tool-specific operating modes thanks to TKM self-control for the AB 250 Standard and Automatic models
Operating principle
Aerosol Boosters create an oil/air mixture with liquid particle sizes in the nanometer range. As a result, the particles are in floating condition and can be easily transported even over longer distances and rotating spindles. Spindle speeds of more than 40,000 rpm can be realized.
The tool with its - compared to the supply line - small cooling channels acts like a nozzle. Here, the incoming aerosol is accelerated to a very high rate - with a simultaneous drop in pressure. This causes the aerosol to condense, i.e., air and liquid segregate and the desired lubricating and cooling effect occurs at the cutting edge of the tool.
Air and lubricant consumption are essentially dependent on the tool as well as the operating pressure and can be preciesly adjusted.
The process requires no moving parts, no complex micro-dosing devices and no internal electronics. Therefore, our devices are characterized by highest reliability and at the same time best possible cost-effectiveness.
Fields of application
In addition to turning and milling, successful applications include:
- Thread forming
- (Deep hole) drilling
- Circular milling
- Spindling with single- and multi-blade tools
- Broaching
- Machining of composite & sandwitch materials
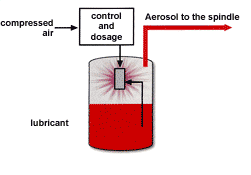
TKM Self-Regulation
Each tool requires a specific lubricant quantity and an optimum lubricant-to-air ratio, both of which depend, for example, on the cooling channel diameters and various process boundary conditions such as the material to be machined and the current material removal rate. Setting these dosing parameters optimally and controlling them individually for each tool or process step is not trivial. The AB 250 Standard and AB 250 Automatic models therefore feature the tried-and-tested TKM self-control system for autonomous control of lubricant metering.
The system is based on the individual aerosol dynamic pressure that builds up in each tool depending on its cooling channels and the respective cutting process. Our devices use this dynamic pressure for the purely pneumatic control of the installed aerosol generators on the basis of an adjustable dosing characteristic curve. Lubricant quantity and lubricant-to-air ratio are thus controlled internally in a continuously variable manner, depending on the process and the tool. Years of experience of tool manufacturers, machine builders and users have gone into the development of the underlying characteristic curve. The ideal lubrication parameters have been determined for a large number of tools and processes and converted into a standard characteristic curve. During initial setup of your system, the standard characteristic curve can be fine-tuned for your individual process, if necessary, by means of two pressure regulators.
The result: The ideal lubricant dosage is automatically set for each tool - without the need for external control or internal electronics. To control the units with TKM self-control, all that is needed after setup is an electronic signal to switch lubrication on/off.
Please do not hesitate to contact us:
Technical support: +49 (0)721 573789 or support@tkm-systems.com
Quotation requests: info@tkm-systems.com